Mastering Quality with SPC: A Guide for Modern Manufacturers
If you're building products on a factory floor, you know that consistent quality doesn't happen by accident. It's the result of tightly controlled processes and constant vigilance. That's where Statistical Process Control (SPC) comes in. It's a proven method that helps manufacturers track what's happening on the line—in real time—and spot potential issues before they become expensive problems. This guide delves into what SPC is, its significance in manufacturing, and how Kanoa MES integrates SPC to enhance quality management.
What Is Statistical Process Control (SPC)?
When most people think of Statistical Process Control (SPC), control charts probably come to mind. And for good reason—they're a central and visible part of how SPC is applied. But SPC is actually a broader category of statistical techniques used to monitor and control a process. It includes not only control charts, but also tools like histograms, run charts, and capability analysis. The core idea is to use data from the production process to understand variation, spot patterns, and identify when things are starting to go off track. Done well, SPC gives teams the insight they need to make timely adjustments and keep quality on target.
At its core, SPC distinguishes between two types of process variations:
-
Common Cause Variation: Inherent in the process and expected.
-
Special Cause Variation: Arises from specific, identifiable sources and may indicate a problem.
By identifying and addressing special cause variations, manufacturers can prevent defects and ensure consistent product quality.
Why and How SPC Is Used in Manufacturing
SPC is integral to modern manufacturing for several reasons:
-
Early Detection of Issues: By continuously monitoring processes, SPC allows for the early identification of deviations, reducing the likelihood of producing defective products.
-
Process Optimization: Analyzing process data helps in understanding variability, leading to more stable and efficient processes.
-
Cost Reduction: Preventing defects reduces waste and rework, leading to significant cost savings.
-
Compliance and Standards: SPC supports compliance with industry standards and regulations by providing documented evidence of process control.
Key Tools in SPC
Several tools are commonly used in SPC to monitor and analyze processes:
-
Control Charts: Visual representations of process data over time, highlighting variations and trends.
-
Histograms: Graphs showing the distribution of data, useful for understanding process behavior.
-
Pareto Charts: Identify the most significant factors in a dataset, following the 80/20 rule.
By leveraging these tools, manufacturers can make informed decisions to enhance process control and product quality.
The Business Case for SPC
Quality isn't just a technical concern—it's a business imperative. Every part that falls out of spec, every product that gets scrapped or reworked, and every customer complaint that needs resolution adds up to real cost. SPC provides a systematic way to reduce those costs by tightening control over the production process and enabling earlier intervention when things begin to drift.
The value of SPC shows up in multiple places:
-
Less Scrap and Rework: Identifying process shifts early prevents material waste and reduces the burden on downstream teams.
-
Fewer Quality Holds and Downtime Events: Proactive quality management avoids the need to stop production to investigate issues.
-
Stronger Customer Trust: Consistent, reliable output builds confidence with OEMs and end customers alike.
-
Data-Driven Continuous Improvement: SPC surfaces trends and patterns that would otherwise go unnoticed, giving CI teams actionable insights.
In short, SPC isn't just about quality—it's about running a smarter, leaner operation with measurable impact on the bottom line.
SPC in Action: How Kanoa MES Empowers Quality Management
Kanoa MES leverages techniques and tools from SPC throughout our application—from using Pareto Charts in Kanoa Ops to break down downtime causes, to applying Control Charts and Histograms in Kanoa Quality to analyze check sheet data. In this article, we'll focus on how SPC tools are used within Kanoa Quality to help teams monitor process stability, spot anomalies, and improve their quality outcomes.
Comprehensive Data Analysis
Within Kanoa MES, the Check Details screen allows users to analyze all check item values within a check sheet. Users can filter results by asset, item, date range, and more, enabling targeted analysis. The table view offers various analytical measures, including minimum, maximum, average, and standard deviation, providing a comprehensive overview of process performance.
Trend View with SPC Rules
Kanoa MES offers a Trend View feature, enabling users to visualize data over time through time series or histograms. This view supports the application of Nelson and Western Electric SPC Rules, which are industry-standard guidelines for identifying out-of-control conditions. For advanced users, Kanoa also supports custom rule configurations, allowing teams to define and apply their own logic for detecting anomalies based on their specific process needs. When these rules detect anomalies, the system highlights them on the chart, allowing for immediate attention and corrective action.
Flexible Charting Options
Users can switch between different charting options to suit their analysis needs:
-
Time Series: Displays data points over time, including calculated upper and lower control limits.
-
Histogram: Shows the distribution of collected data, with detailed counts for each bar.
-
Bar Chart: Visualizes data in bar format, useful for comparing different data sets.
-
Tabular View: Presents raw data in a table for detailed examination.
Additionally, users can export trend data to CSV files for further analysis or reporting purposes.
Conclusion
Statistical Process Control is a powerful methodology for maintaining and improving product quality in manufacturing. By integrating SPC into its MES platform, Kanoa provides manufacturers with the tools needed to monitor processes, identify issues early, and implement corrective actions promptly. This integration not only enhances product quality but also contributes to operational efficiency and cost savings.
Embracing SPC through Kanoa Quality equips manufacturers with a proactive approach to quality management, fostering continuous improvement and competitive advantage in the marketplace.
You May Also Like
These Related Stories
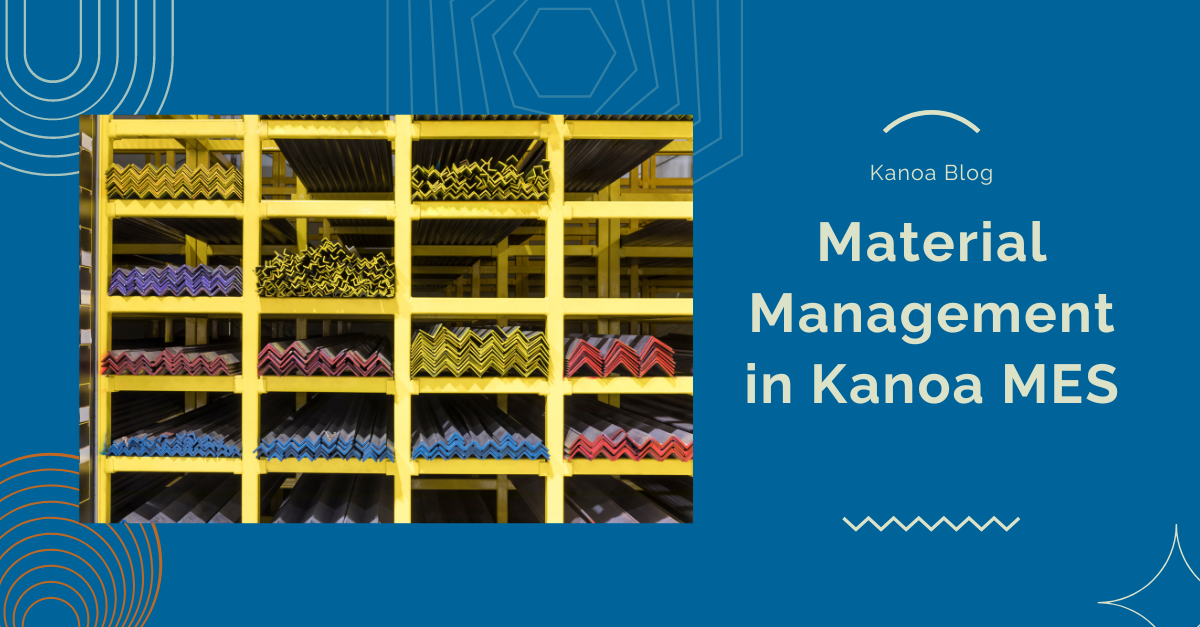
Material Management in Kanoa MES
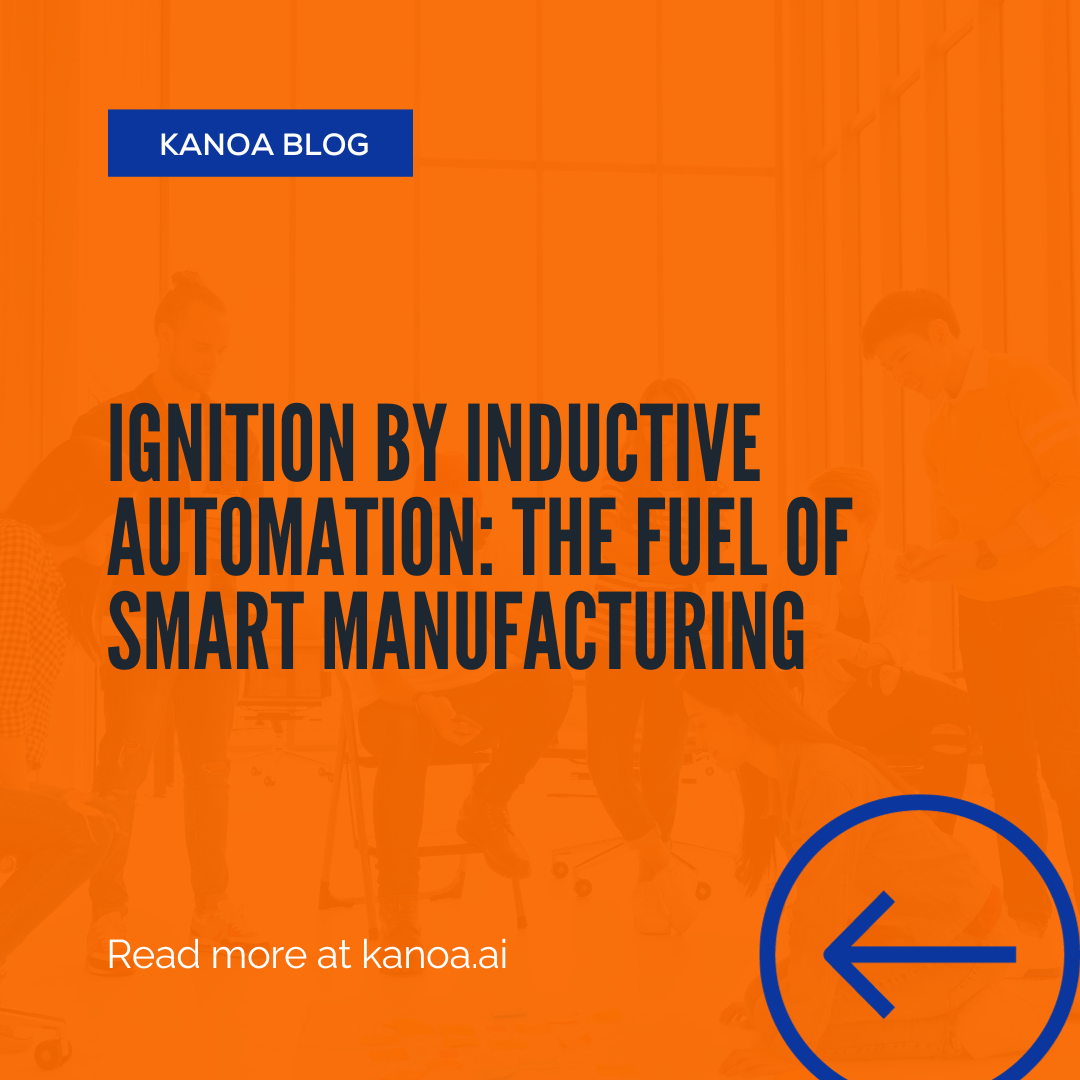
Ignition by Inductive Automation: The Fuel of Smart Manufacturing
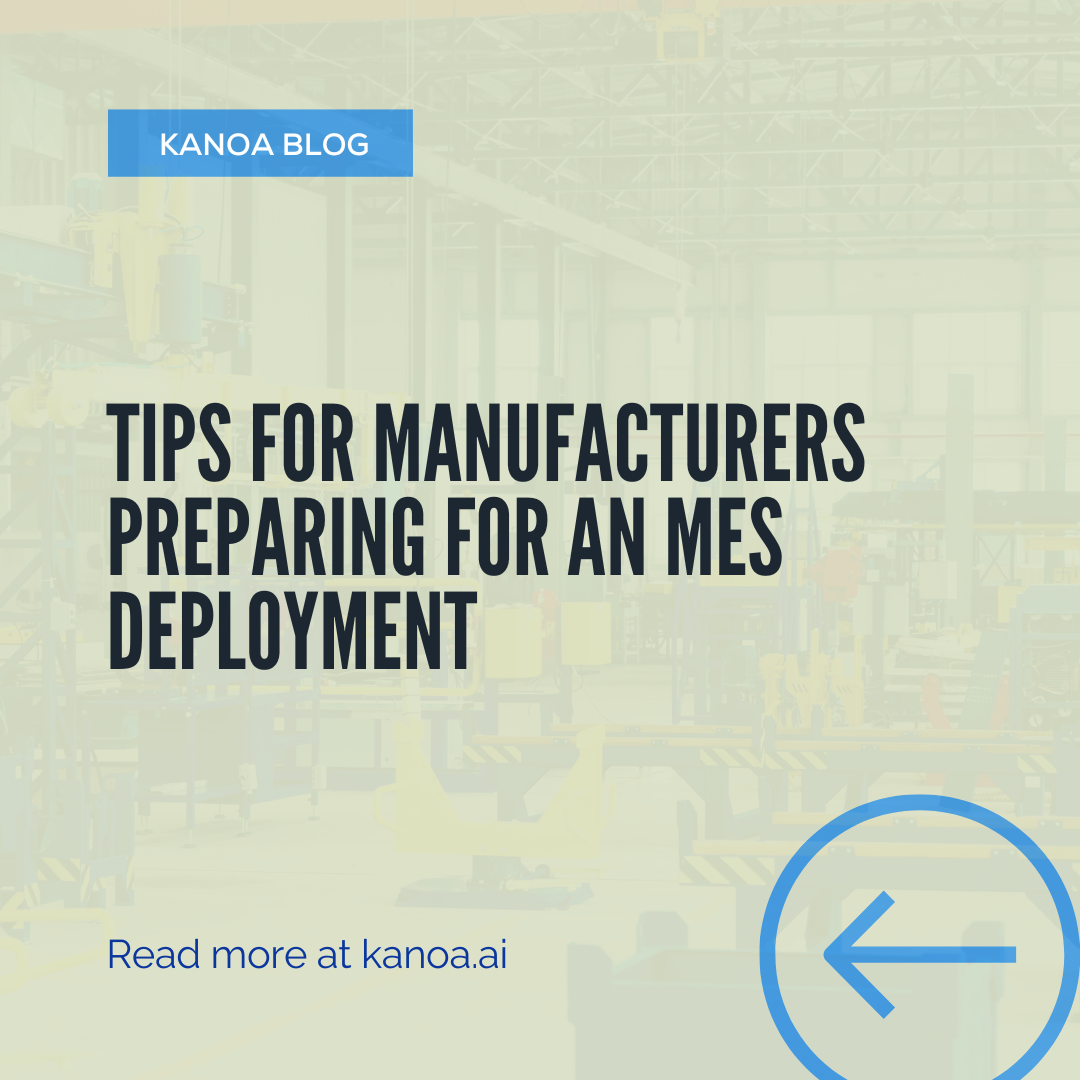
No Comments Yet
Let us know what you think