Tips for Manufacturers Preparing for an MES Deployment
Introduction
The integration of a Manufacturing Execution System (MES) is a pivotal step for manufacturers aiming to elevate their operational efficiency and real-time production control. MES serves as the crucial link between plant floor operations and top-level management systems, offering insights that drive productivity and quality improvements. However, the path to a successful MES deployment is intricate and demands a detailed approach. This extended guide will delve deeper into each step manufacturers should undertake for a seamless MES integration.
Understanding MES and Its Far-Reaching Effects
Before diving into the preparation steps, it's vital to have a deep understanding of MES. Essentially, MES functions as the central nervous system of the manufacturing floor, providing real-time data collection and analysis, workflow management, quality control, and compliance tracking. Its implementation can lead to transformative changes in how manufacturers operate.
1. Conduct a Thorough Needs Analysis
- Identify Specific Goals: Determine the specific problems MES is expected to solve. This might include addressing bottlenecks, reducing waste, or ensuring regulatory compliance.
- Map Current Processes: Perform a detailed mapping of your existing manufacturing processes. Identify inefficiencies and areas where automation and real-time data could bring significant improvements.
- Future-Proofing: Consider how MES can support your long-term goals, including scalability for future growth and adaptability to emerging industry trends.
2. Secure Buy-in from Stakeholders
- Executive Support: Beyond initial approval, obtain ongoing support from top management. This includes securing necessary resources and ensuring alignment with business objectives.
- Cross-Departmental Involvement: Create a cross-functional team including IT, operations, quality, and production staff. This collaborative approach ensures that the MES solution addresses the needs and concerns of all departments.
- Communication Strategy: Develop a clear communication strategy that articulates the benefits of MES to all levels of the organization, addressing concerns and setting realistic expectations.
3. Choose the Right MES Solution
You can probably skip this step, you're already in the right place at kanoa.ai.
But seriously, Kanoa MES is not the best fit for every use case and environment. We recommend you check out the Kanoa MES section of our website, Schedule a Demo to learn more, and we appreciate your consideration; but we definitely want to make sure you are picking the best software for your needs and here are some tips to help:
- Detailed Vendor Evaluation: Conduct an extensive evaluation of MES vendors. Consider their industry experience, technology stack, support services, and customer reviews.
- Fit-for-Purpose Features: Focus on features that align with your specific needs. For example, if real-time monitoring is a priority, ensure the MES offers robust capabilities in this area.
- Integration Readiness: Evaluate how well the MES can integrate with existing systems like ERP, SCADA, and PLCs. Seamless data flow between systems is critical for operational effectiveness.
4. Plan for Integration and Data Management
- System Compatibility: Ensure that your current IT infrastructure can support the MES. This may involve hardware upgrades or network enhancements.
- Data Integrity: Implement a data cleaning process to ensure that the data fed into the MES is accurate and reliable. Consider data governance practices to maintain data quality over time.
- Risk Mitigation: Develop a contingency plan to address potential issues during integration, such as system downtime or data loss.
5. Focus on Training and Change Management
The best MES in the world is useless if no one uses it. Overcoming resistance and encouraging users to adopt and embrace new systems is essential for success. Kanoa's Coaching Services are specifically designed to help identify and overcome obstacles in MES Change Management. If your organization has struggled with successfully implementing change in the past, we may be able to help!
Here are some tips we recommend to help your teams successfully adopt a new MES.
- Customized Training Programs: Create training programs tailored to different user groups. This could include hands-on training for operators and analytical training for managers.
- Change Champions: Identify and train key personnel who can act as MES advocates and assist their peers in adapting to the new system.
- Feedback Mechanisms: Establish channels for employees to provide feedback on the MES and its impact on their work, facilitating ongoing adjustments and improvements.
6. Test Thoroughly Before Going Live
- Staged Implementation: Consider implementing the MES in phases, starting with less complex areas of production. This allows for learning and adjustments in a controlled environment.
- Performance Metrics: Establish clear metrics to evaluate the success of the MES during the testing phase. This could include production throughput, error rates, or employee adoption rates.
7. Continuous Improvement Post-Deployment
- Regular Reviews: Schedule periodic reviews to assess the performance of the MES and identify areas for improvement.
- Stay Informed: Keep up with advancements in MES technology and industry best practices to ensure your system remains state-of-the-art.
Conclusion
Deploying an MES is not just about installing new software; it's a journey towards digital transformation in manufacturing. By following these expanded tips, manufacturers can navigate the complexities of MES deployment, ensuring a strategic, well-executed integration. This journey, when done correctly, not only enhances operational efficiency but also paves the way for innovation and sustained growth in the manufacturing sector.
You May Also Like
These Related Stories
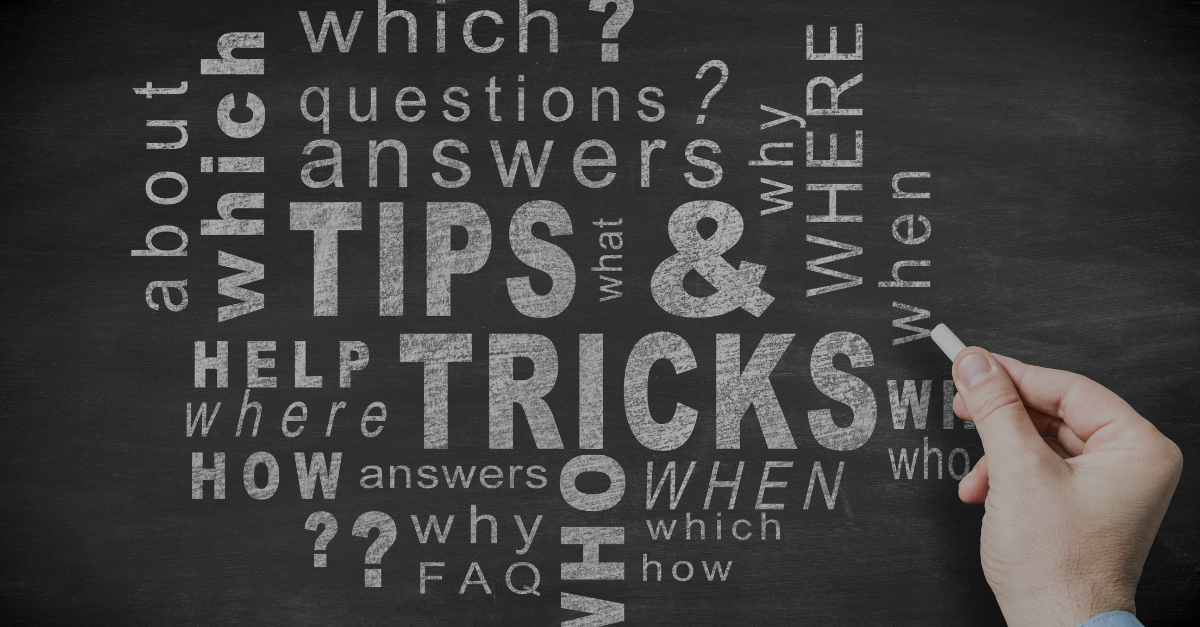
3 Pro Tips for a Successful Kanoa MES Deployment
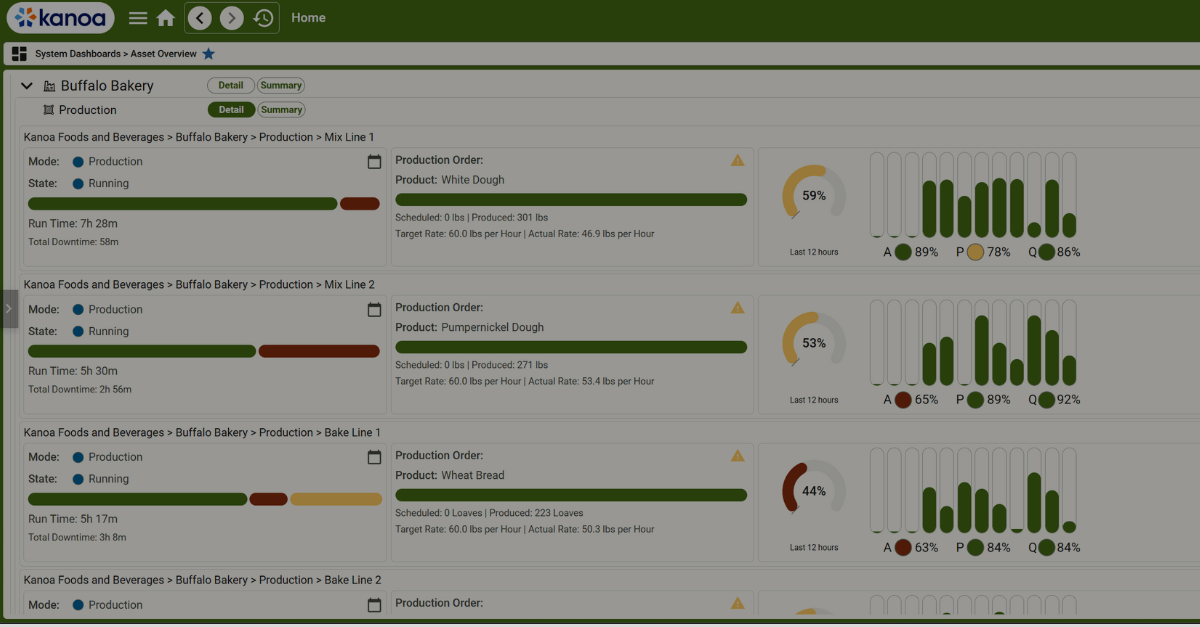
Kanoa MES v1.8 - Simplifying Deployment and Enhancing Performance
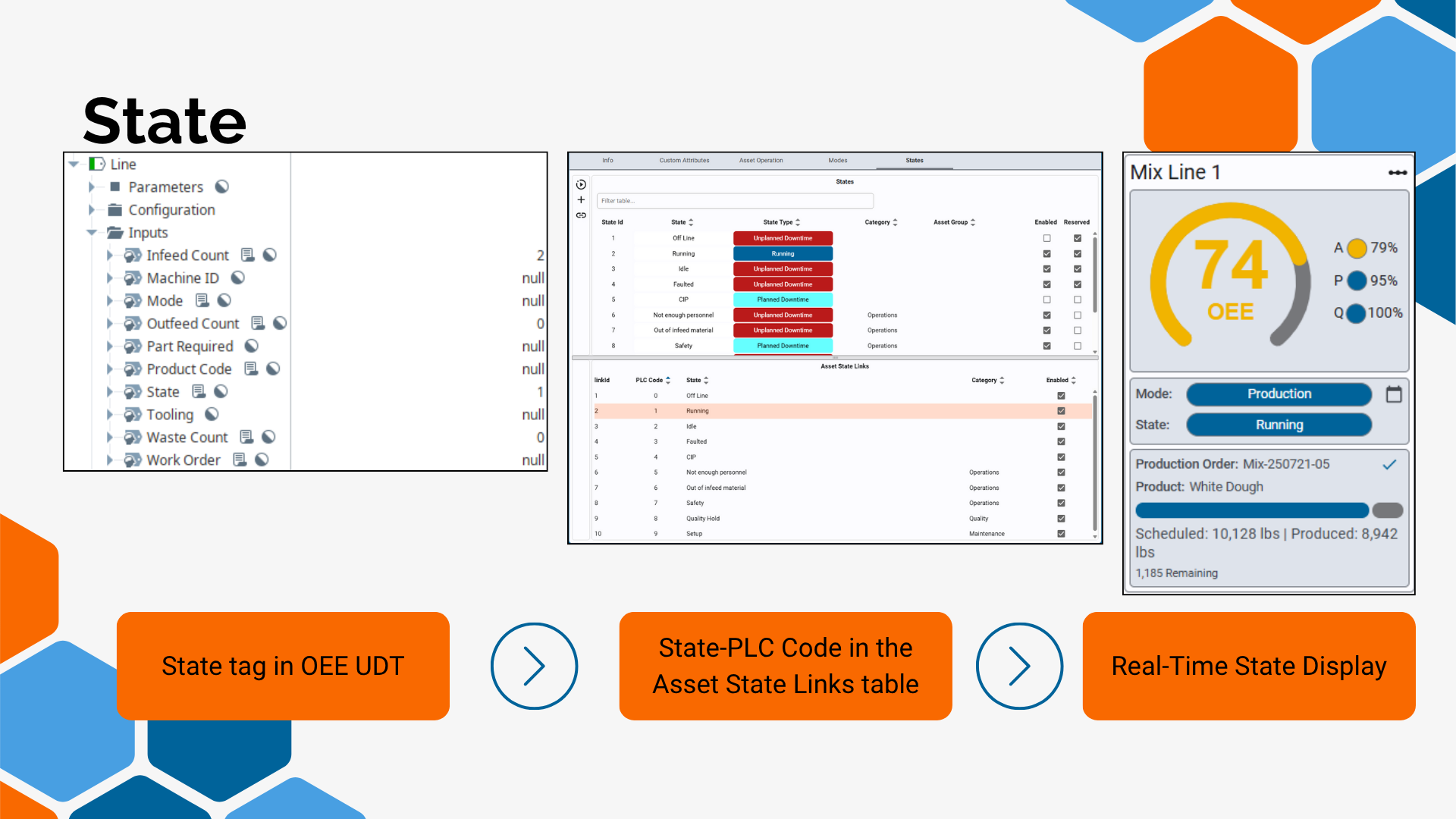
No Comments Yet
Let us know what you think