Lots in Kanoa Ops: Enhancing Production Tracking and Insights
At Kanoa, we constantly innovate to provide solutions that enhance operational efficiency. One of our recent advancements in Kanoa Ops is the introduction of "Lots." This blog delves into how Lots function within Kanoa Ops and how they can be leveraged to improve your manufacturing processes.
What Are Lots?
Lots are useful for identifying and managing specific units of production within your manufacturing operations. In Kanoa Ops, a Lot is a unit of production with its own unique identifier, material, quantity, and timestamp. Lots can be used to track machine infeed or outfeed, can be assigned states like OK, Hold, or Scrap, and given a Reason like "Bad Color." Lots allow manufacturers to gain valuable insights into how products move throughout their plant, aiding in better management and optimization of production processes.
Key Components of Lots
- Unique Lot Number: Each lot is assigned a unique identifier to distinguish it from others.
- Status and Reason Codes: Lots have statuses such as OK, Hold, or Scrap, along with reason codes providing more detailed explanations (e.g., Quality Recheck, Potential Contamination).
- Item: Lots are often associated with an Item or Material configured in Kanoa Ops.
- Quantity: Each lot is associated with a specific quantity and unit, critical for accurate production and material tracking.
- Timestamp: A timestamp records when each lot event occurs, ensuring accurate tracking over time.
- Source and Destination: Indicates whether the lot is an infeed or outfeed, affecting the materials available for selection and processing.
- Lot Events: Various events (e.g., weight association, material composition) are tracked for each lot, providing detailed insights into its history and status.
Practical Applications of Lots
Manual Entry and Production Tracking
Lots offer a versatile solution for manual data entry, essential for operations where automated systems might not capture the full scope of production activities. For example, operators can manually weigh materials and enter these weights into the system, ensuring accurate recording of production outputs.
Kanoa recommends using Lots for manual entry of infeed, outfeed, and scrap to make it easier to correct mistakes and edit data after-the-fact. Kanoa's Manual Entry Line screen demonstrates how you can implement Lots to have a Kanoa Ops asset run entirely by Manual Entry; a great solution for legacy equipment or to act as a stop-gap while you are waiting for more automated data.
Waste Recording
Lots play a significant role in waste recording, enabling manufacturers to specify and manage waste accurately. Each lot can denote a specific amount of input or output as waste, with associated waste reasons and operator comments. This can be done via manual entry or through automatic configuration in Kanoa Ops to create waste lots with the appropriate waste-coding. By tracking waste this way, manufacturers can gain detailed insights into waste sources and reasons, facilitating more effective waste reduction strategies.
Lot Transfers
Lots can be transferred between different areas or stages of production. For instance, a large batch of material can be divided into smaller lots for processing as needed, facilitating better inventory management and workflow optimization.
Influencing Production Counts
Lots can influence production counts in two primary ways:
-
Counter Updates: By enabling the counter function when creating a lot, the system can automatically update infeed, outfeed, and waste counters based on the lot's quantity. This feature allows for pseudo-real-time manual entry, where data is updated as it is entered, rather than at the end of a shift or production run.
- Real-Time Updates: Operators can enter data for in-feed, out-feed, and waste counters in real-time, ensuring that production counts are always up-to-date and accurate.
- Improved Accuracy: By manually updating counters, operators can ensure that the recorded data reflects actual production activities, reducing discrepancies between machine-calculated counts and actual outputs.
-
Reconciliation: This feature allows users to compare automatic counts with manually entered lot data and reconcile discrepancies. Users can choose to replace, add, or subtract counts based on lot data, providing flexibility to accommodate various manufacturing scenarios.
- Flexibility: Users can select specific lots to include or exclude, adjust weights, and scale lot quantities to influence production counts as needed.
- Post-Production Adjustments: Reconciliation is not in real-time but provides the flexibility to make adjustments after data entry, ensuring accurate final production counts.
Benefits and Future Prospects
The introduction of lots in Kanoa Ops brings several advantages:
- Enhanced Production Insights: Gain valuable insights into how products and materials move through your plant.
- Improved Waste Management: Accurately record and analyze waste, leading to more effective waste reduction strategies.
- Flexible Inventory Management: Transfer and manage lots across different stages of production with ease.
- Scalable for Future Features: As we develop more traceability features, the lot system will seamlessly integrate, enabling comprehensive traceability solutions.
In conclusion, the lot system in Kanoa Ops is a powerful tool for enhancing production tracking and insights. While we aim to automate as much as possible, lots provide a robust solution for manual entries and tracking, ensuring that manufacturers have the flexibility and accuracy they need to optimize their operations. Stay tuned as we continue to expand our traceability features, making Kanoa Ops an even more indispensable part of your manufacturing process.
You May Also Like
These Related Stories
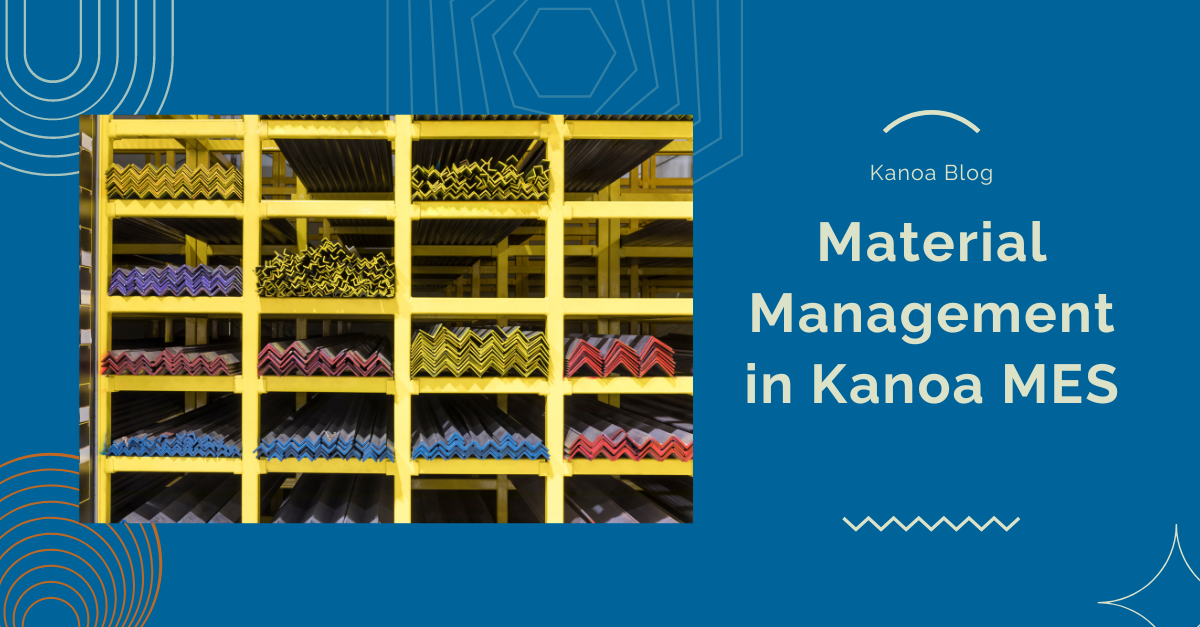
Material Management in Kanoa MES
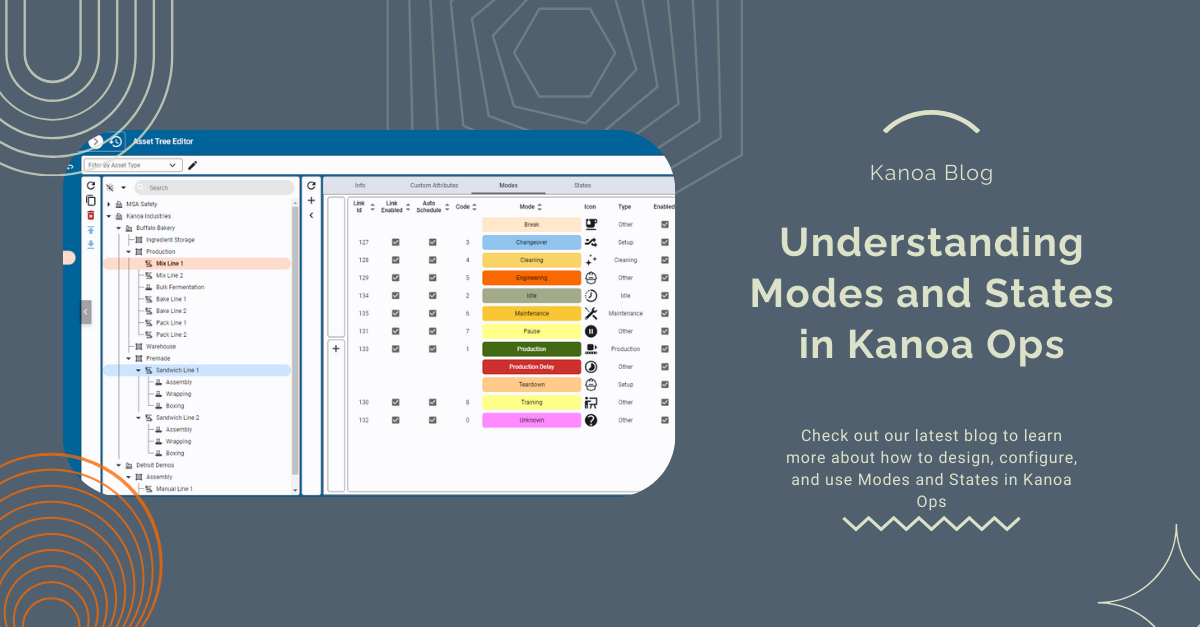
Understanding Modes and States in Kanoa Ops
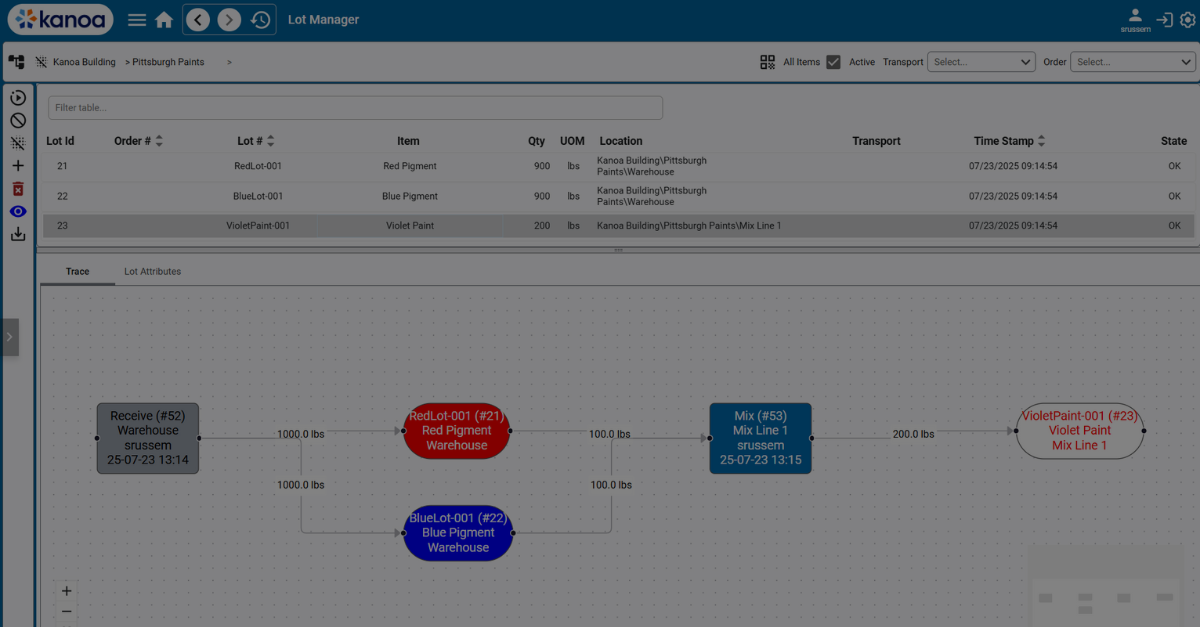
No Comments Yet
Let us know what you think