3 Tips for Using Kanoa Ops to Drive Continuous Improvement
Once you’ve installed Kanoa Ops and begun generating data for your plant, the next step is leveraging that data to drive meaningful, ongoing improvements. A well-structured approach ensures your team can maximize efficiency, address bottlenecks, and sustain operational excellence. Here are three pro tips to help you make the most of Kanoa Ops within your continuous improvement strategy.
Tip 1: Establish New Rituals and Habits to Review Your Data
It’s natural to focus on immediate data—"How am I running now?" or "How did I run yesterday?"—to make real-time adjustments. However, to fully capitalize on the insights Kanoa Ops provides, you should also build structured habits for reviewing long-term performance trends.
How to Review Data Effectively:
- Analyze Weekly OEE Trends: Use the OEE tracking tools in Kanoa Ops to assess week-to-week performance over the past three months. Identify specific shifts, lines, or times of day where performance consistently falls short.
- Monitor Product-Specific Performance: Over a longer time horizon, review whether certain products consistently underperform compared to targets. Identifying these trends can reveal opportunities for process optimization.
- Leverage the Run Review Feature: Kanoa Ops makes it easy to analyze both short- and long-term data to uncover patterns that inform strategic decisions.
Turn Insights Into Action:
Schedule regular review meetings with your team to discuss these findings. A monthly performance review session can help identify recurring bottlenecks and develop actionable strategies for improvement. Embedding these habits into your workflow ensures that the data from Kanoa Ops directly contributes to process optimization.
Tip 2: Create Dashboards for Shift-Standup Meetings
Shift-standup meetings are a key opportunity to align your team on priorities, recent performance, and upcoming tasks. By customizing dashboards in Kanoa Ops, you can ensure that the most relevant data is always front and center, improving decision-making and collaboration.
Key Dashboard Components:
- Downtime Summaries and Notes: Review downtime incidents from the previous shift to address recurring issues promptly.
- Performance Trends: Display recent production trends to celebrate improvements or highlight areas needing attention.
- Upcoming Schedules: Provide visibility into the next set of production runs, ensuring the team is aligned and prepared.
Expanding Dashboard Use:
Dashboards don’t have to be limited to shift meetings. Consider tailoring dashboards for other key functions, such as:
- Management Reviews: Aggregate broader performance KPIs to assess overall efficiency.
- Production Planning: Integrate data on inventory levels and forecasted demand to refine scheduling decisions.
With dashboards providing real-time insights, your team can spend less time compiling reports and more time acting on the data.
Tip 3: Empower Your Team to Own Continuous Improvement
Kanoa Ops isn’t just a tool for managers—it’s a resource for your entire team. When employees at all levels understand how to access and interpret key performance metrics, they can play an active role in improving operations.
Ways to Encourage Employee Engagement:
- Train Staff on Key Metrics: Educate operators and supervisors on how to analyze OEE, downtime, and quality data to spot inefficiencies.
- Encourage Ownership of Improvement Areas: Assign team members responsibility for tracking and enhancing specific processes, such as maintaining throughput consistency or reducing downtime causes.
- Create a Feedback Loop: Provide a structured way for employees to submit observations and improvement ideas based on the data. Leadership should review and act on these insights to reinforce a culture of continuous improvement.
Recognizing and implementing team-driven ideas not only enhances efficiency but also fosters a data-driven mindset across the organization.
Conclusion
By integrating these three tips into your daily, weekly, and long-term workflows, you can unlock the full potential of Kanoa Ops to drive continuous improvement. Establishing structured review habits, utilizing customized dashboards, and empowering your team ensures that your data translates into actionable improvements. With Kanoa Ops, you have the tools to make informed decisions and achieve measurable results in your manufacturing operations.
You May Also Like
These Related Stories
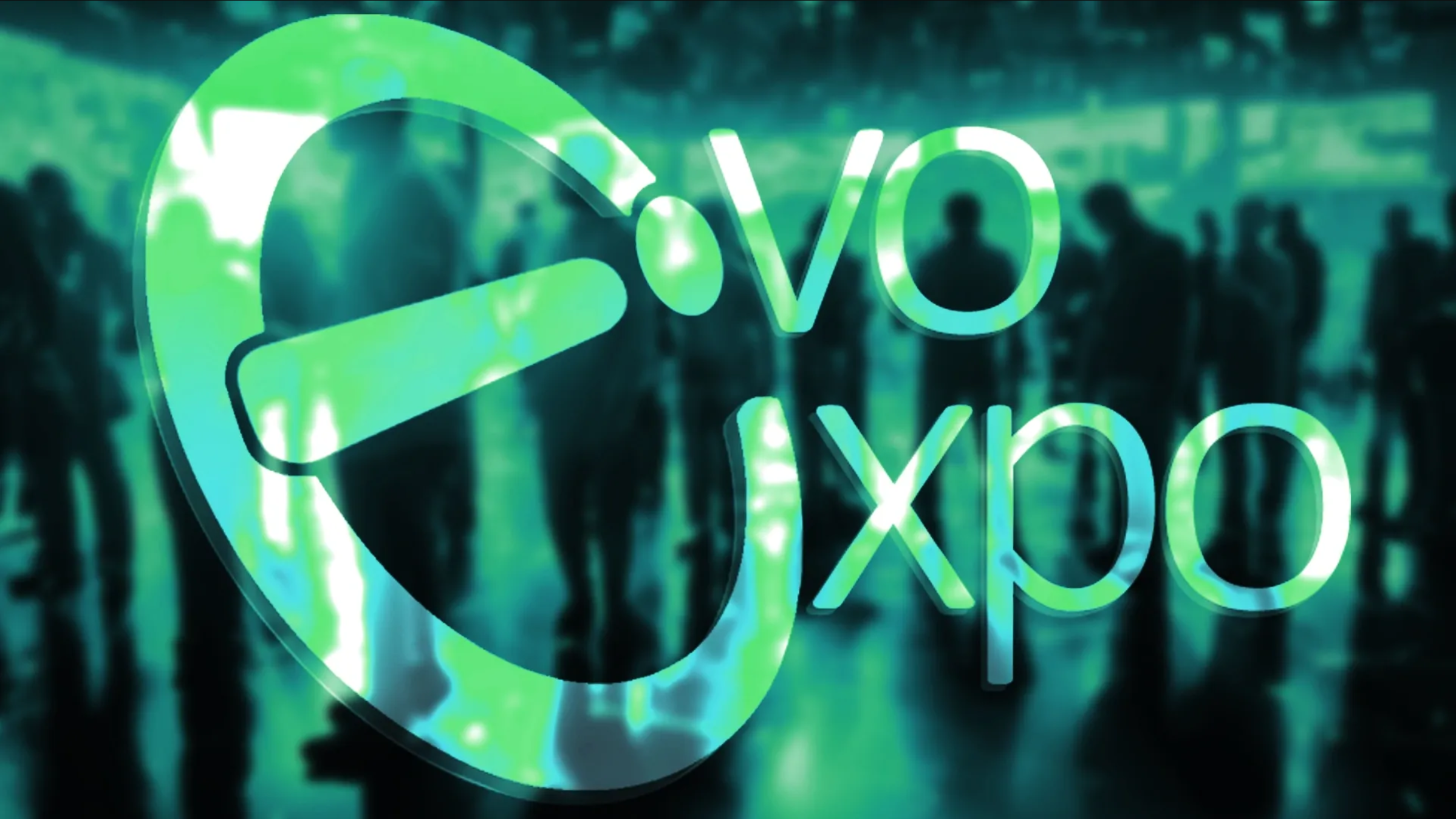
Kanoa is Heading to EVO Expo 2025!
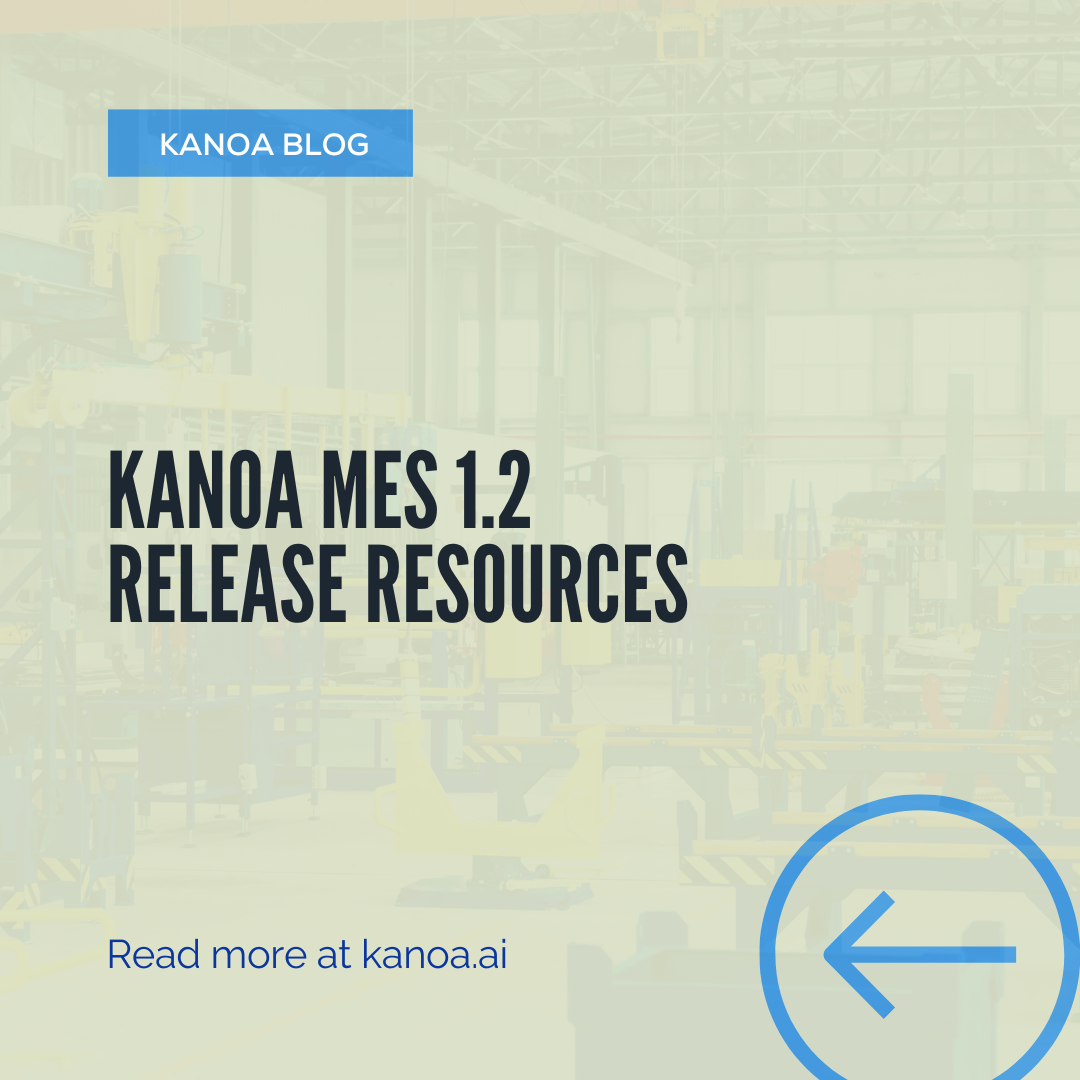
Kanoa MES 1.2 Release Resources
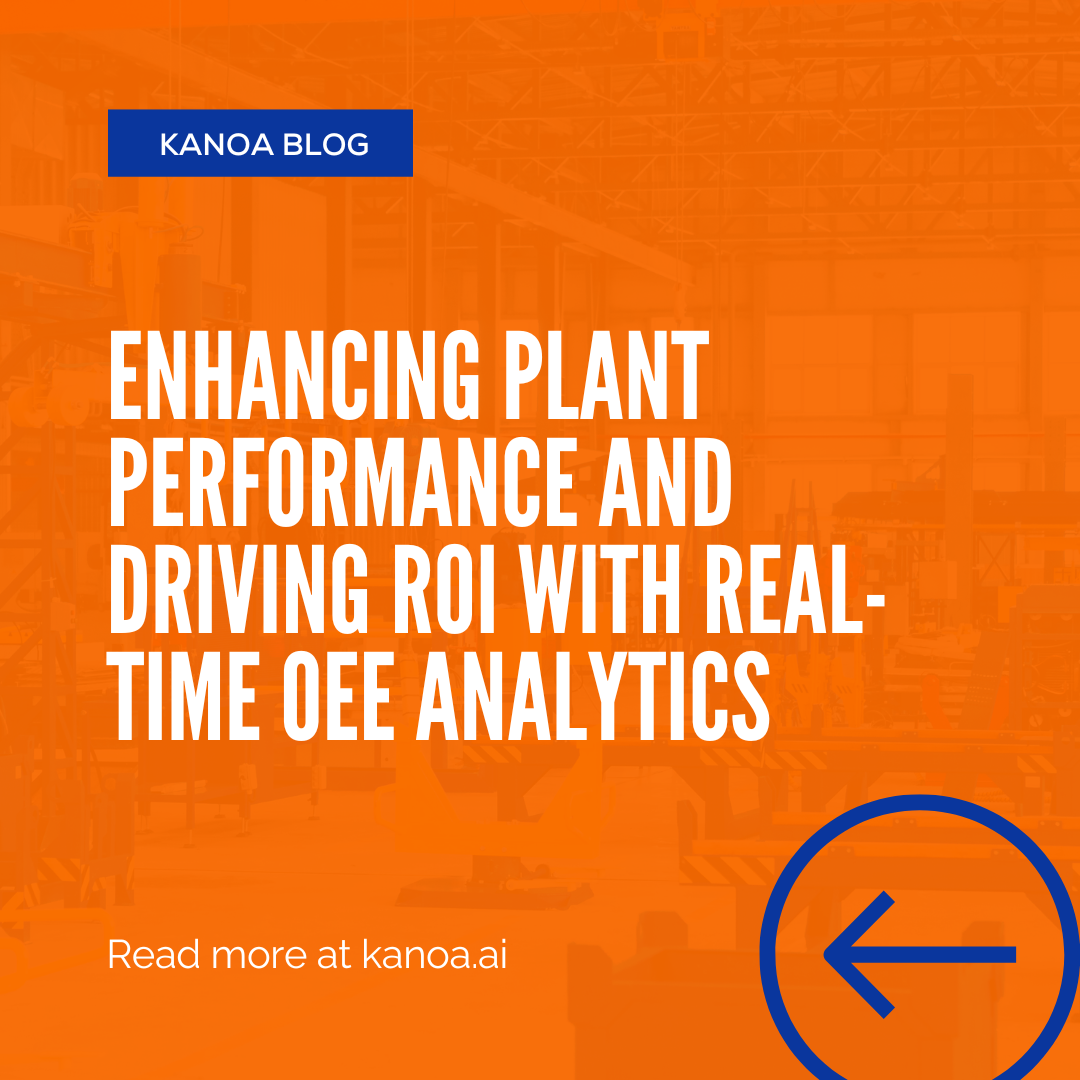
No Comments Yet
Let us know what you think