ANSI/ISA-95 is a 5-part standard that is designed to provide consistency in manufacturing terminology, information models, and application functionality. The ISA-95 Equipment Hierarchy model (in Part 1: Models and Terminology) and its “Purdue model,” is one of the most commonly used models to explain the technology stack to run a plant and can be considered required reading for any Smart Manufacturing 101 course.
While there’s a lot more to the ISA-95 standard than the hierarchy, it is a great place to get started to understand what an MES is and where it fits into the system architecture of a factory:
- Level 0 represents the physical production process itself: how we make things. The physical process is turned into digital information using sensors and signals on the manufacturing line.
- Level 1 represents the sensing and manipulation layer, where we are using control systems like PLCs to read sensor data and react with automated control signals.
- Level 2 represents the monitoring and supervising layer. This is where humans interact with SCADA and HMI systems that visualize the production process and can issue machine or system-level commands.
- Level 3 represents the Manufacturing Operations Management layer, which is where our MES software lives. This can be thought of as the “orchestration” layer of the plant, where we’re managing all logistics, machines, operators, schedules, and inventory of the plant.
- Level 4 represents the business planning and logistics layer. This layer includes business systems designed to manage multiple factories and processes to take in customer orders and deliver manufactured products.
This automation pyramid is an elegant visualization that summarizes the most common architecture for factories and their control systems. It is particularly useful for understanding the role of an MES. Levels 0-2 are very controls-focused. These are usually the “Mission Critical” systems: if something goes wrong here, the factory is not producing. Level 4 is also usually well-understood: Enterprise Resource Planning (ERP) systems are usually a company’s first foray into software to help connect their business systems to manufacturing processes.
The Manufacturing Operations Management, Level 3 layer is commonly thought of as what ties the Mission Critical Level 0-2 systems together with the business context of Level 4 systems. It is usually the “highest level” system responsible for managing plant level data and communicating that with enterprise-level business systems. It is also an orchestration system, designed to take the logistics information from those enterprise systems and present it in a way that makes sense for the plant-level.
We often joke in MES/MOM circles: every manufacturer has a MES, or else nothing would ever get made. It’s just that many manufacturers’ “MES” is composed of emails, Excel spreadsheets, and hard-working people who need to manually schedule, coordinate, and analyze their work.
So, what does MES software actually DO sitting there between Level 2 and Level 4? That’s where the rest of the ISA-95 standard comes into play. There are activity models to show how Production, Quality, Inventory, and Maintenance processes work and interact. There are process segment definitions to help define how work is performed. This is the real “meat” of the standard; impossible to summarize in a short blog, but definitely recommended for anyone serious about an MES implementation.
Why is this important for your MES implementation? Well, there are some that would say that you need to really understand your plant operations in the context of the ISA-95 standard before you start an MES implementation; especially since so many MES software providers create their software according to the rules and practices laid out in ISA-95. But there are some drawbacks to that strategy: manufacturers can spend months or even years working to understand their plant through the context of a model like ISA-95. ISA-95 can provide a great framework for understanding and characterizing plant operations, but it should not hold you back from implementing new technology or realizing continuous improvement.
That’s why Kanoa encourages manufacturers to know the standard and understand why it is important, but not to stress if they find the standard does not fit their current mentality, operations, or entire business model. ISA-95 is only a guide, and it should be applied where it is useful and ignored when it is not useful.
So if you’re new to the MES world and just learning about ISA-95, you’re on the right track and should continue to explore the standard and how it applies to your environment. But if you’re struggling to make the connections between the standard and your process, that is OK and there are a lot of Industry 4.0 and MES technologies you can still apply to improve your factory.
You May Also Like
These Related Stories
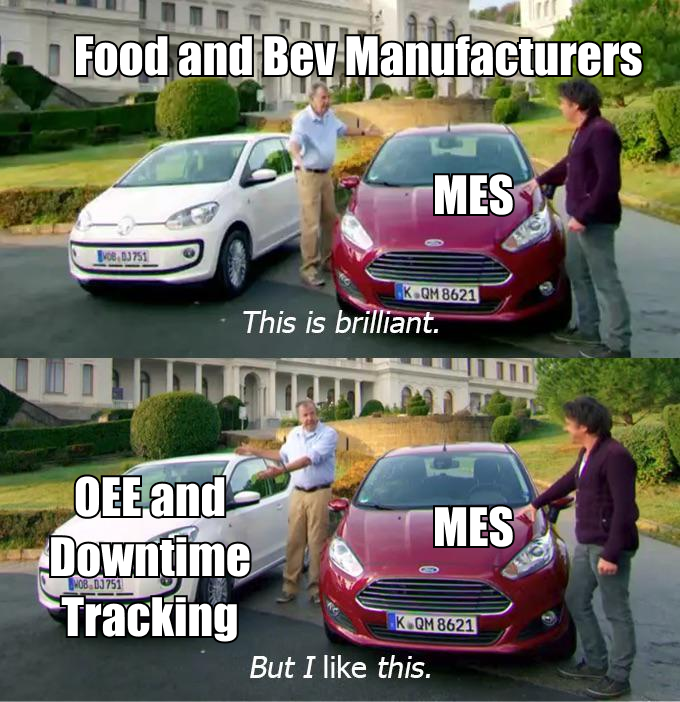
What's in a name? MES Across Industry Verticals
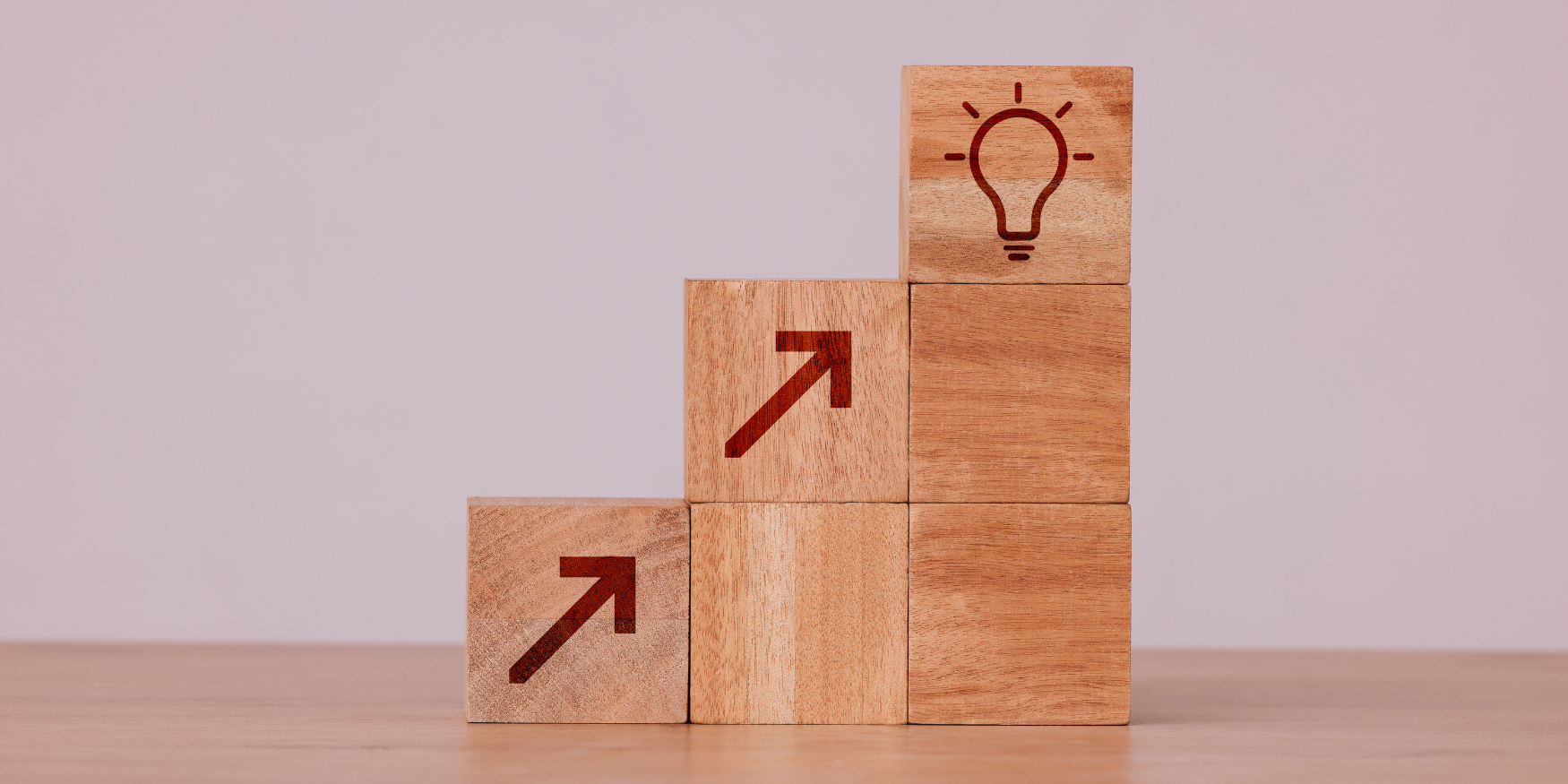
What's in a name? Findings and Conclusions
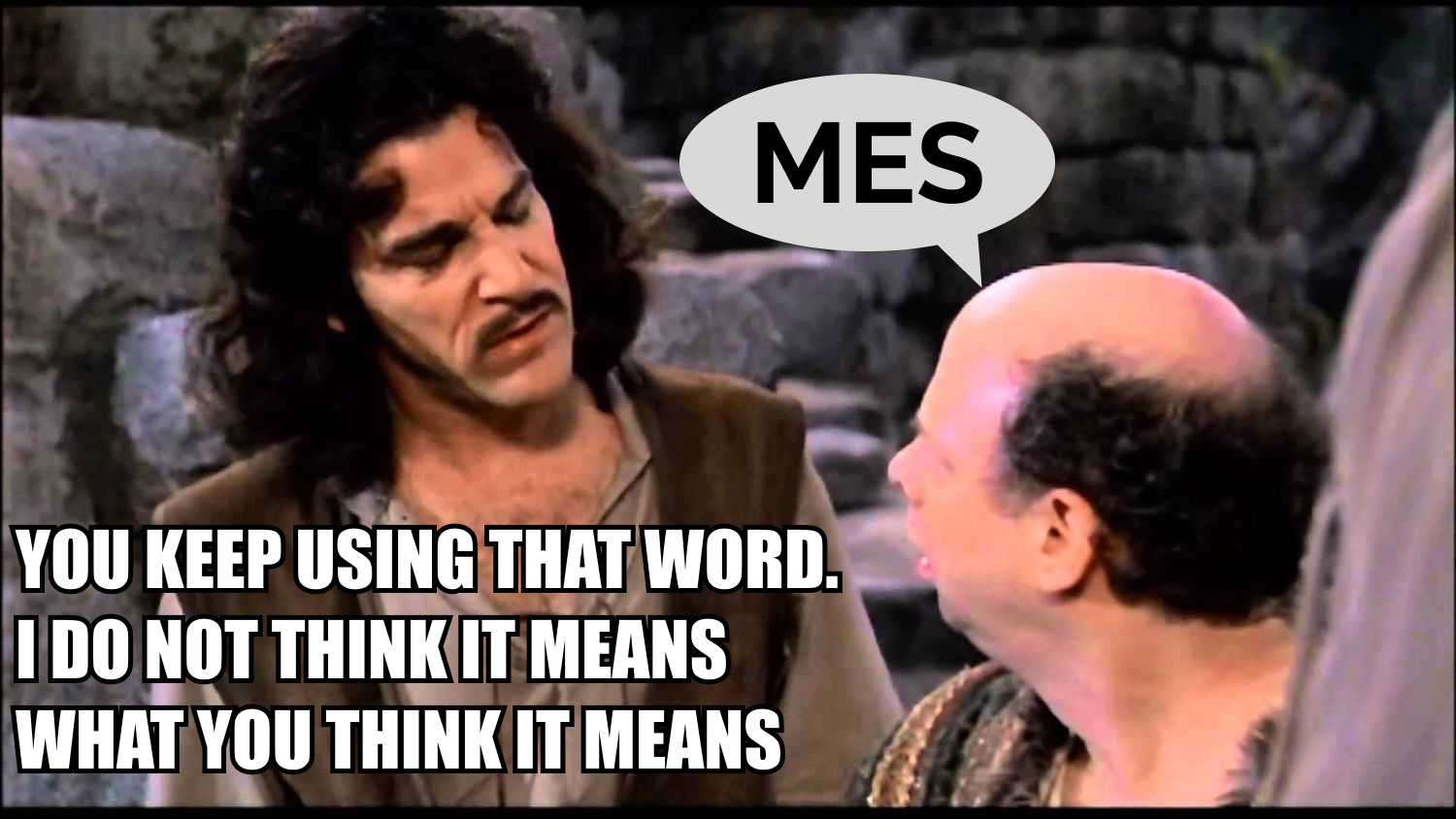
No Comments Yet
Let us know what you think